Brent Beach: Grinding and Keeping your edge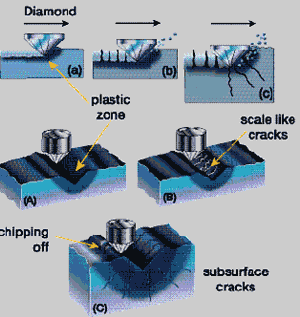
Грубые абразивы повреждают металл на глубину в 3 раза большую, чем глубина рисок, которые они оставляют.
Тонкие абразивы (1мкм. и тоньше) не разрушают кристаллическую структуру металла. Изображение выше уже упоминалось в "general discussion of bevels".
Рассмотрим сначала случай, когда вы произвели обдирку с выходом на РК.
Царапины, оставленные абразивом, продолжаются до кромки. Металл под дном царапин, вплоть до 3х глубин царапины, был поврежден. Кристаллическая структура была разрушена силой зерна, срезающей металл.
Во время последующей заточки вы стачиваете металл до дна самой глубокой царапины.
Поскольку все визуальные признаки наличия рисок от обдирки более не прослеживаются, вы начинаете думать, что работа первым точильным абразивом завершена.
Неправильно. Все еще остался слой металла, который был деформирован во время обдирки.
Вы не можете увидеть этот ущерб. Деформированный металл выглядит как недеформированный металл.
В лаборатории деформации обнаруживаются с помощью мягкого кислотного травления. Эти кислоты разъедают деформированный металл быстрее, чем прочный металл. При большом увеличении зоны деформации становятся видимыми в виде долин, лежащих в основе первоначальных глубоких царапин. Предположение, что металл, который выглядит гладким, не деформируется, привело к ошибочной теории истирания металла, связанной с именем Beilby Layer.
Рассмотрим следующий случай, когда вы шлифуете почти до выхода на РК, но не выходите.
Металл на РК сохраняет структуру, которая была у него, когда его в последний раз точили.
Если вы используете набор абразивов 3M, который я использую, последний абразив составляет 0,5 микрона. Абразивы до 1 микрона практически не вызывают подповерхностной деформации. Предполагая, что древесина не содержит слишком много кремнезема, изнашивание металла на краю во время использования не добавляет никакой деформации - кристаллическая структура и, следовательно, прочность стали сохраняется.
Если не было деформации на этапе обдирки, то и удалять нечего. Как только сформируете правильную геометрию абразивом - вы закончили.
Стачивание металл лишь до получения заусенца не поможет вам преодолеть поврежденный слой.
Вы можете получить заусенец даже до того, как вы удалите все царапины от шлифования. Что случается задолго до того, как вы удалили поврежденный металл. Надежда на то, что наличие заусенца означает, что вы готовы к следующему шагу хонингования - это ложная надежда.
Таким образом, выход на РК на стадии обдирки значительно усложняет процесс заточки.
Если вам не удастся удалить весь поврежденный металл - кромка будет изнашиваться быстрее.
Больше времени, больше шагов шлифования, ... Для того, чтобы удалить весь поврежденный металл, вам нужно стачивать гораздо дольше.
Хуже того, нет видимых признаков того, что вы удалили достаточно металла. Наличие заусенца недостаточно.
Вы можете подумать, что ускоряете процесс заточки, выходя на обдирке на кромку, но вы либо гарантируете дефектный слой стали на кромке, либо очень растягиваете процесс заточки, без возможности знать, когда уже можно остановиться.
ПРИМЕЧАНИЕ. Эта диаграмма(рис. выше) подверглась критике как неприменимая к металлам, поскольку материал, удаляемый при истирании стали, похож на стружку, в то время как на этом рисунке показаны мелкие частицы (пыль из драгоценных камней). Суть этой диаграммы не в форме удаляемого материала, а в том, что осталось позади. А конкретнее - разрушение кристаллической структуры ниже дна царапины. И сталь, и драгоценные камни имеют кристаллическую структуру. Обе кристаллические структуры одинаково реагируют на истирание.
В настоящее время известно, что периодическое формирование полос интенсивного сдвига является неотъемлемой частью образования механической обработки стружки, и неизбежно, что части этих полос включаются в создаваемую новую поверхность.
-- Leonard Samuels - Metallographic Polishing by Mechanical MethodsИсходник:Large abrasives damage the metal up to 3 times deeper than the bottoms of the scratches they leave. Very small abrasives (in the 1 micron range and below) do not shatter the crystal structure of the metal. This diagram is also discussed in the general discussion of bevels.
Consider first the case where you grind through the edge. The scratches left by the abrasive continue to the edge. The metal below the base of the scratches, up to 3 times the depth of the scratch, has been damaged. The crystal structure has been disrupted by the force of the grit shaving off metal.
During honing, you hone away metal to the bottom of the deepest grinding scratch. With all signs of the grinding scratches gone, you may think you are finished with the first honing abrasive. Wrong. There is still a layer of metal that was deformed during grinding. You cannot see that damage. The deformed metal looks just like undeformed metal. In the lab the deformations are detected by use of mild acid etching. These acids attack deformed metal more quickly than sound metal. Under high magnification the deformation zones become visible as valleys underlying the original deep scratches. The assumption that metal that looks smooth is not deformed led to an erroneous theory of metal abrasion associated with the name Beilby Layer.
Consider next the case where you grind almost to the edge. The metal at the edge retains the structure it had when it was last honed. If you use the set of 3M abrasives I use, the last abrasive is 0.5 micron. Abrasives under 1 micron cause almost no subsurface deformation. Assuming the wood does not contain too much silica, the wearing away of the metal at the edge during use does not add any deformation - the crystal structure and hence the strength of the steel is retained. Not having caused any deformation by a grinding step, you have none to remove. Once you hone to the correct geometry, you have finished.
Honing until you get a wire edge does not get you past the damaged metal. You can get a wire edge even before you have removed all of the grinding scratches. That is long before you have removed the damaged metal. Hoping that the presence of a wire edge means you are ready for the next honing step is a false hope.
In summary then, grinding through the edge makes honing far more difficult. If you fail to remove all the damaged metal, you have an edge that will wear faster. More sharpening, more grinding steps, ... In order to remove all the damaged metal you have to hone for much longer. Worse, there is no visible indication that you have removed enough metal. The presence of a wire edge is not enough.
You may think you are speeding up the sharpening process by grinding through the edge, but you are either ensuring inferior steel at the edge, or a very long honing step with no means of knowing when to stop.
NOTE: This diagram has been criticized as not applicable to metals because the material removed during abrasion of steel is shaving like, while this picture shows small particles (gemstone dust). The point of this diagram is not the shape of the material removed, it is what is left behind. Specifically, the fracturing of the crystal structure below the bottom of the scratch. Both steel and gemstones have a crystal structure. Both crystal structures react in the same way to abrasion.
The periodic formation of bands of intense shear is now known to be intrinsic to the formation of machining chips, and it is inevitable that parts of these bands are incorporated in the new surface being generated.
-- Leonard Samuels - Metallographic Polishing by Mechanical Methods
Источник:- Brent Beach: Grinding and Keeping your edge
- Leonard Samuels - Metallographic Polishing By Mechanical Methods, Fourth Edition, 2003.
//первоисточник - подробнее