Но я хочу поговорить несколько о другом - о тестовых объектах, подходящих для оценки разрешающей способности микроскопных объективов. Многие пользуются препаратами с панцирями диатомовых, известных видов, с известными параметрами, например, но их не всегда легко достать, кроме того, если речь про металлографические объективы и характерные же для металлографических микроскопов системы освещения (т.е. освещение через объектив), целесообразнее тестовые объекты, не имеющие покровного стекла. Например, существуют кремниевые слайды со шкалами, в т.ч. субмикронными - изготавливается такое дело методом фотолитографии, сходно с изготовлением микросхем, поэтому субмикронные шкалы не проблема. Очень интересная и полезная штука, но тоже редкая.
Потому важно, чтобы в качестве препарата могло послужить что-то, что и так имеется в хозяйстве. По крайней мере у заточника или у столяра. Лично я использую, иногда, в качестве подобного "тестового препарата" шлифы сталей с известной насыщенностью карбидами и разбросом их размера.
Приведу пример:
Сделал шлиф стали 110Х18МШД от мастерской Андрея Бирюкова. Заявленная твёрдость 60HRC.
Cтруктура выглядит симпатично и, по большей части, наиболее крупные карбиды укладываются в данные, найденные в сети. При том можно говорить о том, что в целом структура достаточно мелкая, по сравнению со многими сталями близкими.
Шлиф изготавливался полностью вручную, это фрагмент хвостовика клинка, также термообработанного, как и собственно клинок.
Готовился к изучению участок около 1,5 квадратных сантиметра. Плоскость была выведена на заточных брусках, затем шлифовка последовательно абразивными шкурками на основе карбида кремния P800-1000-3000 c минеральным маслом Total LUBRILAM S 23 L. Масло показало себя шикарно на шкурках: производительность с ним приближается к производительности шлифовки шкурками с олеиновой кислотой. Шлам легко удаляется со шкурок путём нанесения свежей капли масла и промакиванием поверхности шкурки бумажным полотенцем.
После шлифования шкурками выполнял полировку пастами Luxor на основе электрокорунда, последовательно фракциями со средними точками 6,5мкм., 3мкм., 1мкм., 0,5мкм., втёртыми в офисную бумагу, положенную на притёртую керамику. При втирании пасты в бумагу, для лучшего её распределения и для необходимой смазки во время работы, применялось тоже масло Total LUBRILAM S 23 L.
Для травления использовался аккумуляторный электролит (экспозиция 2 мин.).
Микрофото фрагмента изучаемого участка, с наибольшим количеством наиболее крупных карбидов, с объективом SO Optics LU Plan Fluor 50x0.80 WD 2mm Semi-Apo с Raynox DCR-150 в качестве тубусной линзы на штативе микроскопа МББ-1А с освещением через объектив с помощью осветителя ОИ-17. Масштаб съёмки 52:1, кадрирование, ресайз:
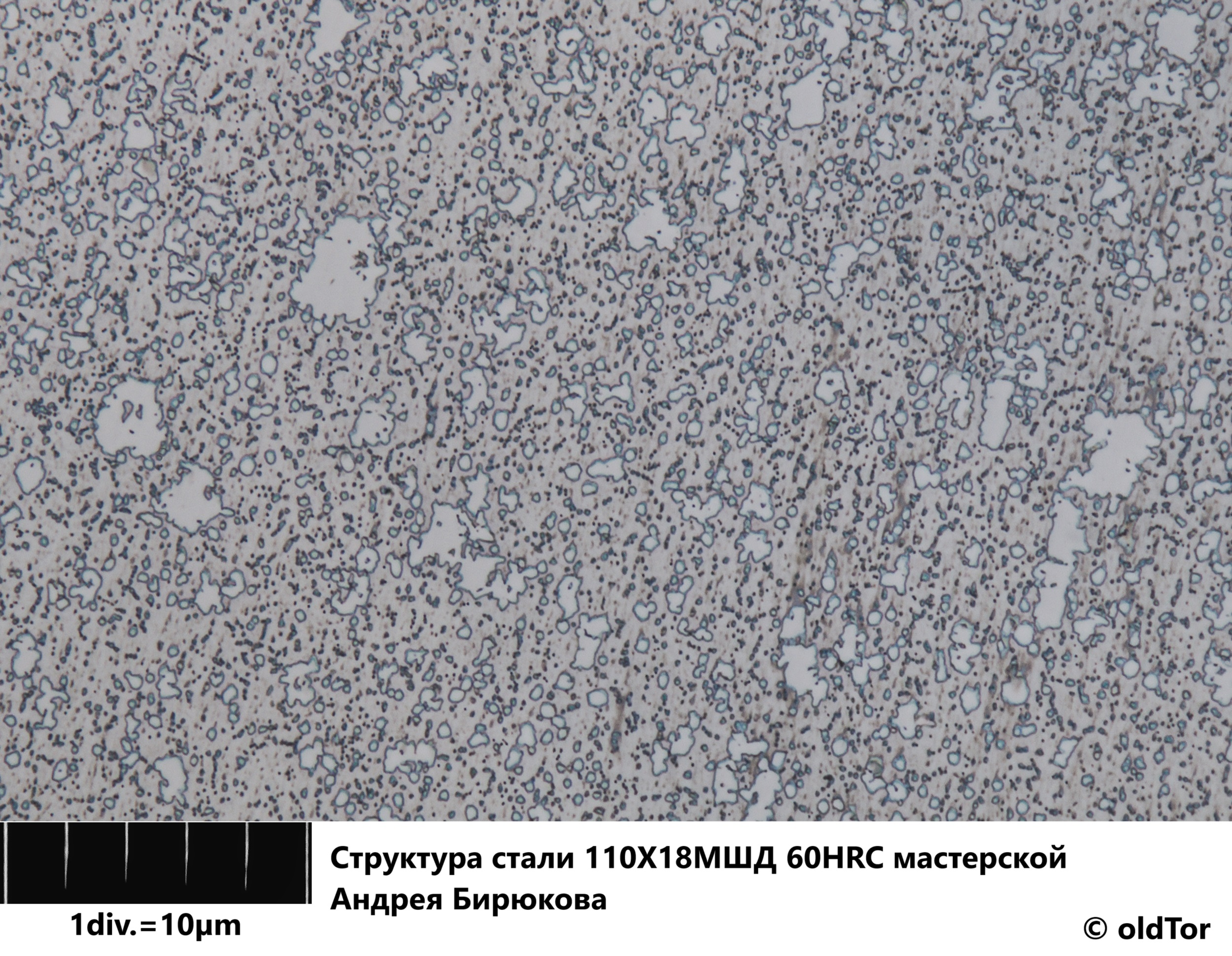
Выбор типа абразивов для шлифования и полирования обусловлен особенностью карбидов в стали - в основном это карбиды хрома, с которыми прекрасно справляется и карбид кремния и электрокорунд, но для облегчения получения высоких классов шероховатости при полировании, целесообразнее на предварительных стадиях выбрать абразив, который более эффективно режет карбиды хрома. В данном случае это карбид кремния. После того, как неровности структуры им эффективно "срезаны", для окончательной полировки совершенно достаточно электрокорундовых абразивов.
Алмазные плёнки и пасты, либо на основе CBN (кубического нитрида бора-эльбора) будут реально нужны на сталях с заметным количеством карбидов ванадия, либо, в некоторых случаях, карбидов образованных молибденом и вольфрамом (например в быстрорежущих сталях типа Р18, Р6М5 и близких).
Для сталей же, где "зёрна" преимущественно представлены цементитом или карбидами хрома, более чем достаточно карбида кремния и электрокорунда.
Из сталей близких представленной на фото, также хорошо для изготовления тестовых шлифов для оценки разрешающей способности неплохо подходят 95х18 (термообработанная на высокую твёрдость - около 60-61HRC), 440С, VG-10 - т.е. весьма широкоупотребительные стали, которые в серийном производстве в целом довольно прилично термообрабатывают и режущий инструмент из которых весьма широко распространён в нашей стране.
Разумеется, для оценки разрешающей, весьма ещё невредно понимать, насколько в показания вмешивается размер пикселя матрицы, насколько он адекватен размеру проекции единицы разрешения на матрицу камеры, но это уже другая история.
Главное, что при достаточно скромном наборе доступных расходных материалов и сравнительно безопасного и доступного травителя, изготовление постоянного тестового объекта не составляет особой трудности, если человек знаком с хотя бы азами абразивной обработки.
Разумеется, крайне полезно иметь объект-микрометр и для облегчения измерений пользоваться его снимком, сделанным в тех же условиях.
Время на изготовление подобного постоянного тестового препарата вручную - от 40 минут до 1,5 часов в зависимости от кривизны геометрии и грубости шероховатости подготавливаемого объекта. Разумеется, при особо кривой геометрии и грубой шероховатости, время на предварительную подготовку существенно увеличивается и целесообразно прибегнуть к механизации, при наличии определённых навыков выполнения таких работ (чтобы всё не испортить перегревом/созданием слишком глубокого дефектного слоя и пр.)
Для тех, кто весьма далёк от абразивной обработки, неплохими тестовыми объектами могут служить казённые образцы классов шероховатости (лучше полученные шлифованием или точением), или поверхности прецизионного измерительного инструмента, для которого заявлены достаточно высокие классы шероховатости, и который проходил ОТК - благо такого инструмента достаточно доступного - хватает. Я долгое время пользовался, к примеру, поверхностями поверочных угольников по классу 1 - очень удобно работать с их боковыми поверхностями, выполненными по 8-му классу шероховатости, используя отражённый свет (через объектив) в т.ч. и с объективами, требующими покровного стекла. Но такой объект хорошо годится для объективов с апертурами, примерно до 0,42 - 0,50. Для более высокоапертурных, желательно что-то более высокого класса шероховатости, дабы рельеф был сопоставим с ГРИП объектива.
Также приведу пример, как раз с поверочным угольником - при базовой длине 0,8мм., параметр шероховатости боковой стороны Ra ≤ 0.63мкм. по ГОСТ 2789, что соответствует 8-му классу шероховатости (иногда - на границе 7-го и 8-го, как следует из сравнительных таблиц, их несложно нагуглить) - микрофото боковой поверхности в отражённом свете (через объектив, с осветителем ОИ-17) с объективом Mitutoyo MPlanApo 20x0.42:
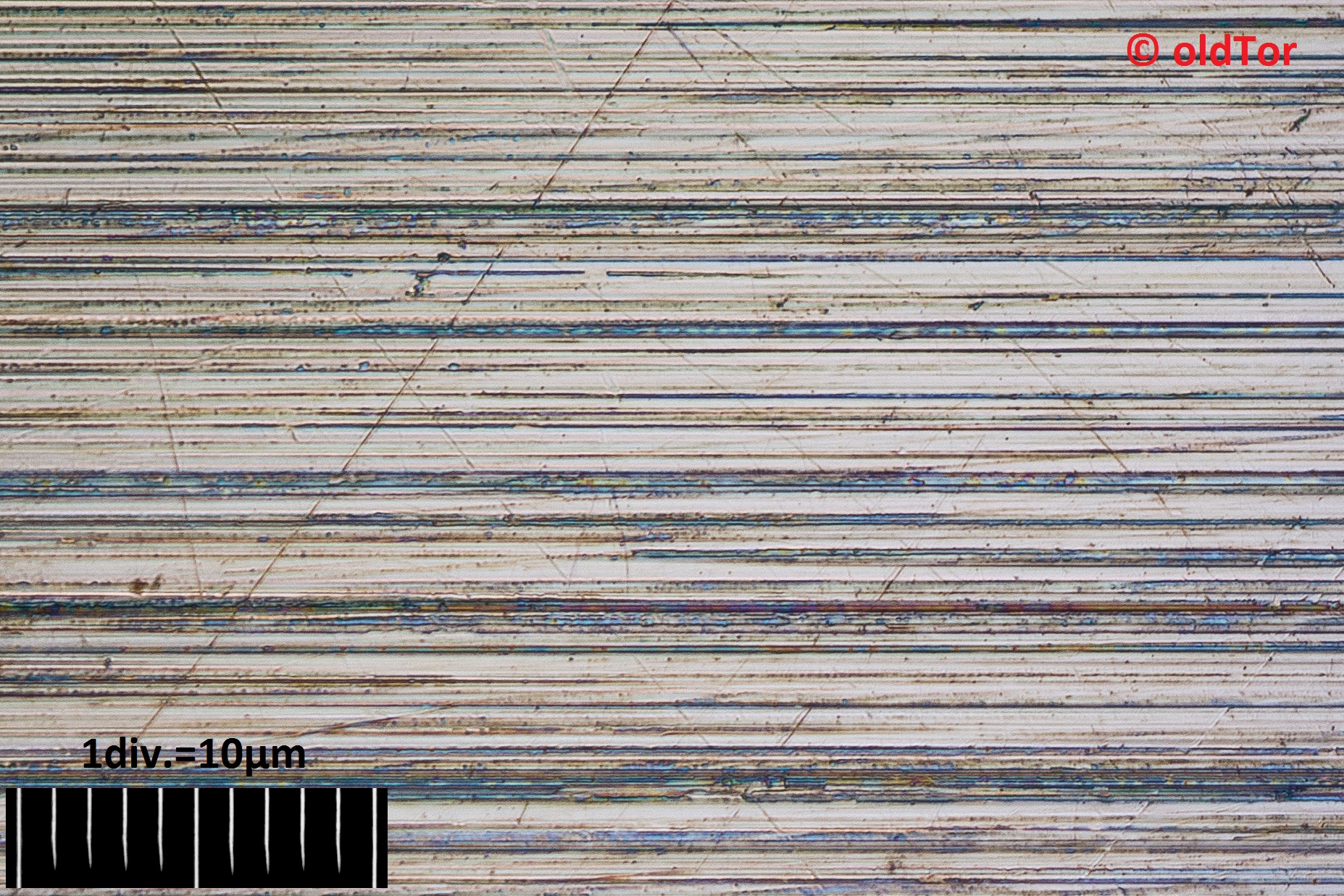
Конечно, хотя я и пользовался угольником аккуратно, на нём есть посторонние царапинки, но они незначительны по сравнению с его собственной шероховатостью, т.е. для оценки поверхность годится.
Наличие оксидных плёнок интерференционной толщины на поверхности стали, повышающих контраст, и достаточного количества близколежащих рисок от обработки, позволяет довольно неплохо использовать такой "готовый вариант" в качестве тестового объекта. Разумеется, эта поверхность не подвергалась никакому дополнительному воздействию - она "как есть".